Replacement Windows & General Contractor Services
Serving Northwest Chicago & Surrounding Areas
What dreams do you have for your home? Masters Touch Exteriors can make them a reality. We can help you make your home special, or we can help you with repairs, maintenance and Roof Replacement Los Angeles. Unless you've recently built your home from your own plans, chances are you have some ideas of what you'd like to do to transform your space to better fit your needs.
"From siding to windows to renovations, Masters Touch Exteriors can handle all of your construction needs."
Masters Touch Exteriors provides homeowners with innovative home remodeling services that stand out from our competitors. Whether you are interested in lowering your heating and cooling costs by having us install new windows, eliminating yearly house-painting costs with our professional siding services, replacing your leaking roof or making a statement with an elegant entryway, Masters Touch Exteriors has a solution for you.
"Why should you choose Masters Touch Exteriors for all of your home remodeling needs?"
Anybody who has ever remodeled has a story. Some have wonderful stories and some have felt the heartache that comes with not doing their homework. The fact is, these problems can be avoided by making sure you choose the right company for the job, the first time.
At Masters Touch Exteriors we go out of our way to produce the best possible results within the amount you have budgeted for your project. Our past work speaks for itself. Click here to view our portfolio.
"Contact Us Today to find out how we can improve YOUR HOME."
Contact Masters Touch Exteriors today and speak with a home remodeling consultant to learn about the products and services available.
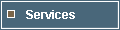 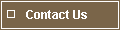
|